In this past week, our team was able come up with three different approaches to how we would sense when switching would take place. All three ideas revolve around the idea of magnets but different sensors will be used that all have their advantages and disadvantages. The three sensors we will consider are hall effect sensors, RFID tags and cards, magnetic sensors (shown below in the mentioned order). The magnetic sensors mounted on the bogie have a great range of use. The only problem with these sensors is the spacing in between the track. The sensors were extremely close to the wall of the track on each opposite side of the bogie and caused scratching of the sensors as the bogie moved on the track. We could not get the RFID tags and cards to work but that will be one of the things my team and I will be working on this coming week. As for the hall effect sensors, we do not own any in the shop and we would like to order some so that we could test the efficiency of all three sensors and decide which of the sensors would work best for both positioning and sensing the magnets mounted on the track. Our team's first choice is the use of RFID tags and cards because it would greatly simplify positioning and sensing of switching. If the bogie could be redesigned a bit so that the magnetic sensors already existent on them could fit better without them scratching on the inside walls of the track, this method could also work satisfactorily.
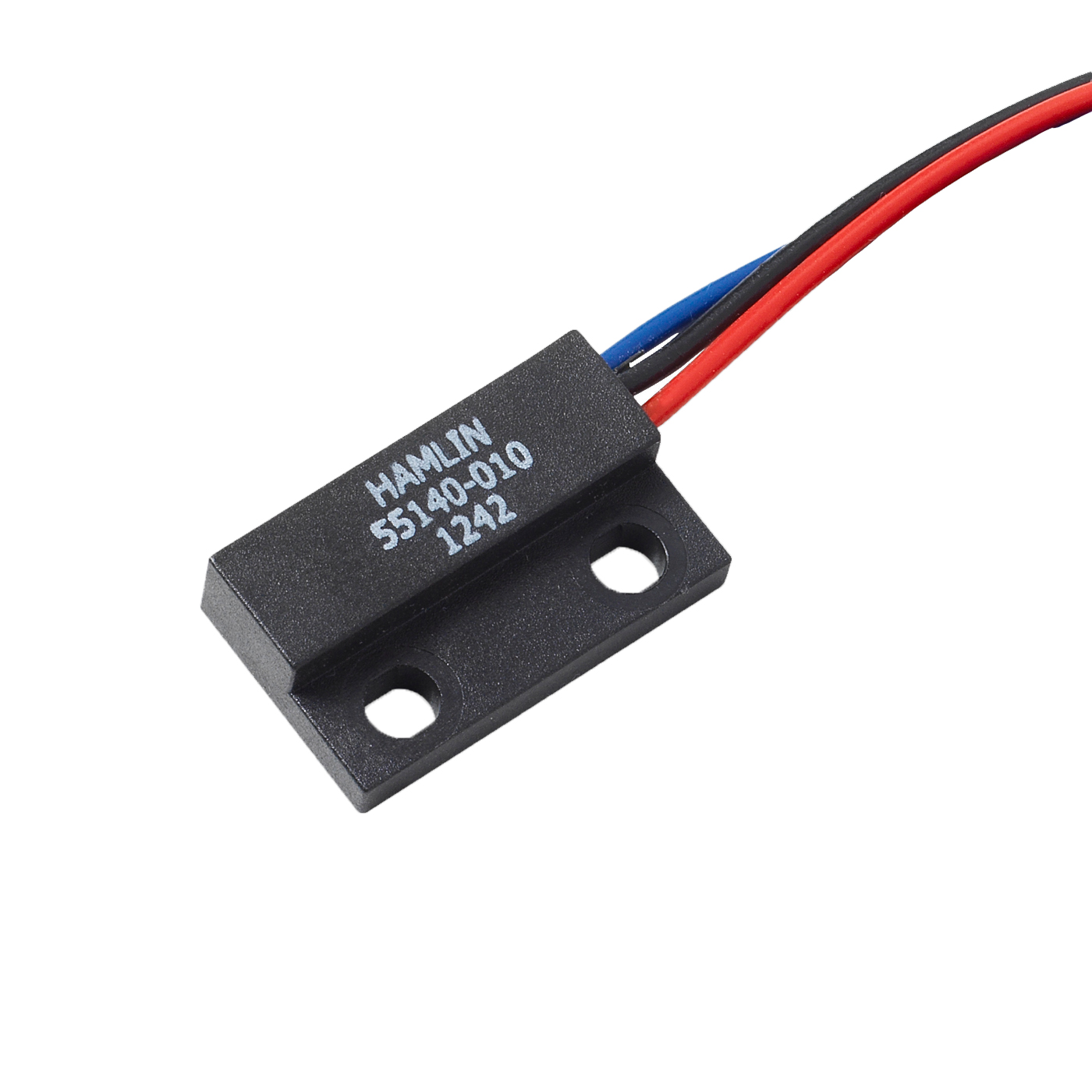


I also helped my team determine where we would need switching to occur and where decision making needs to occur to either make a stop at a station or move to the next loop of the track. We decided that we would need to strategically place the magnets so that if the sensor reads a magnet on the left, the bogie would switch its mechanism from right to left and vice versa. If it reads a sensor on the left, we would need to implement some code based on its destination path if switching to another loop of the track would need to occur. Some of our code has already begun as pseudocode so that we will have a good enough understanding of what the code needs to accomplish.
This week, my team and I have been busy with preparing for our first presentation of the semester and we all hope it goes well. With this mentioned, I was unable to thoroughly go through the Processing software as I said I would do last week but I will make it my priority this coming week so that my team and I can start developing and testing some code so that we can progressively build our code. My teammate Steven had mentioned that he was unable to open the java codes for the Processing software that are on the drive. I am curious to know if I can open the files so that I can study the code and replicate the progress that was made last year. I will look into working with Processing to control a podcar and hopefully be able to get one podcar working with the code uploaded to one of them so that we can fully test the existing podcar and make changes as we see fit. I am looking forward to having our team be done with designing in the next two weeks and start deciding what hardware, tools, and supplies we need to build a successful prototype in the second third of the semester.